Inventory control is an important part of enterprise warehousing management. It aims to reduce inventory levels as much as possible and improve the efficiency of the logistics system by reasonably controlling the enterprise’s inventory levels on the premise of meeting customer service requirements, so as to improve the enterprise’s market share. Competitiveness.
In the process of inventory management, some management misunderstandings often occur. These misunderstandings will lead to the opposite result from the original intention, causing the butterfly effect of chaotic inventory management. Based on these management issues, the following four misunderstandings are summarized for in-depth analysis.
Think of inventory management as warehouse management
From the perspective of the supply chain, inventory is everywhere, including raw material inventory, semi-finished product inventory, work-in-progress inventory, in-transit inventory, finished product inventory, trial product inventory, sample inventory, defective inventory, etc.
In the information age, each physical inventory is usually fed back into the system accordingly. The inventory in the system is not just a simple material number or product number. It is often related to transaction data (incoming and outgoing, movement, quantity, date, responsible person, etc.), associated data (location in BOM, replaceable A series of information such as product information, etc. are bound to each other, making management more complicated.
At the same time, this data is not static. It may change every moment. If the resulting large amount of data is not managed, it can easily cause huge troubles to the supply chain.
What we see through inventory is an end-to-end supply chain, the flow of physical inventory, the flow of inventory information, and the resulting flow of funds associated with the inventory. These are the three major elements of our supply chain: physical flow, information flow and capital flow. Therefore, from a broad perspective, inventory management is to manage the entire supply chain from the perspective of inventory, and its importance is self-evident.
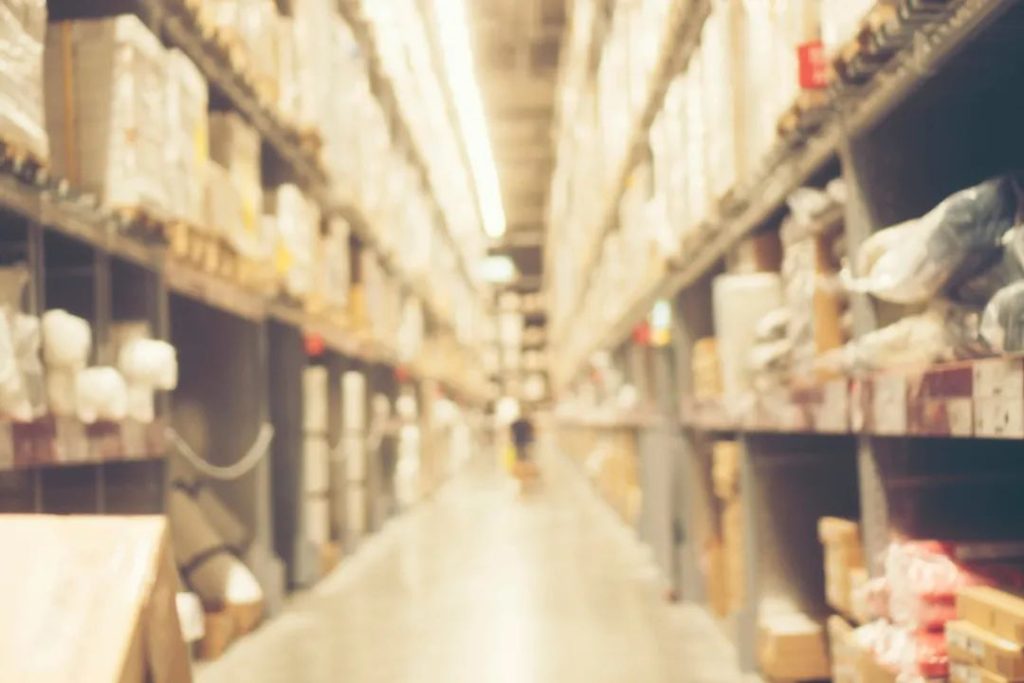
ERP can solve inventory problems
The establishment of information systems (such as ERP) is an important part of the supply chain architecture. As a supply chain architect, you should have a very clear understanding of what ERP can and cannot solve.
First of all, ERP cannot solve the problem of the process itself; secondly, the design and sorting of the process is the key to ERP implementation and is also one of the jobs of the supply chain architect. What’s more important about ERP is the operator. Can the operator use it efficiently?
Solution: First of all, we must understand this. ERP brings efficiency improvements. Processes that were manually operated in the past can be automated through the system, greatly improving timeliness. The inventory problem itself is a process problem, so ERP cannot solve the inventory problems caused by the process, but it can help us improve the efficiency and accuracy of inventory management.
The higher the inventory turnover rate, the better
Improving inventory turnover has many benefits for businesses. It can reduce the net working capital required for business operations and improve the company’s capital utilization; it can also increase the company’s ability to withstand risks in the face of market crises and improve the flexibility of the supply chain. So how to improve inventory turnover rate?
According to the calculation formula of inventory turnover rate: Inventory turnover rate = COGS/average inventory. It is easy to derive from the formula that there are two ways to improve inventory turnover rate: one is to increase sales, and the other is to reduce average inventory. The main way to improve sales is to improve the collaborative efficiency of upstream and downstream, so as to accurately and quickly meet the needs of the sales end with quality and quantity. There are three main ways to reduce average inventory:
- Reduce safety stock;
- Increase delivery frequency;
- Reduce sluggish inventory.
However, the higher the inventory turnover rate, the better. It needs to meet certain prerequisites, that is, the increase in inventory turnover rate will not lead to a decrease in customer delivery satisfaction, and the cost of maintaining flexibility will not exceed The cost pressure that enterprises can bear. Therefore, inventory turnover usually needs to be measured in conjunction with several other indicators.
Manage products in a unified way
Being out of stock for category C products is just as bad as for category A products. This reason will lead to excess inventory of Category C or insufficient inventory of Category A, because only by handling different categories of inventory products differently can efficiency requirements be met. Having the same inventory target for all products assumes that all inventory products are consumed in the same amount and at the same rate, which is certainly not true. Companies with such goals will spend a lot of time digesting Class C inventory. Safety stock amounts are fixed, which also assumes that all inventory products are consumed at the same amount and at the same rate, resulting in inefficient inventory planning.
Use ABC analysis and manage Category A products separately from Category B and Category C products. As mentioned above, only in this way can inventory decisions be linked to real consumer demand. Apply safety time instead of safety stock. Safety time will automatically increase safety stock according to forecast demand, while safety stock is only a fixed value that must be set manually and will not take changes in demand into account.